TOOLING AS AN INTEGRAL PART OF THE A+ PROCESS
Often dismissed as ‘just a cost that needs to be cut’, tooling is more than an expense and plays an impact on the manufacturing success of a program. For die casters with limited technical depth, it is a reasonable stance: even if presented with high-performance tooling, they could not materialize its potential.
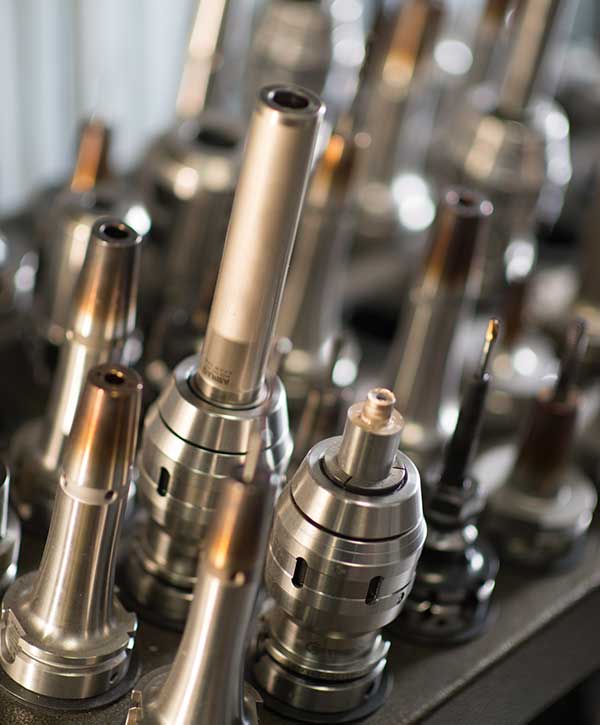
In reality, the tool is a key component on the path to die casting excellence. A better tool means lower cycle times, better part quality, less unpredictable downtime. But a better tool requires more process expertise to deliver on its potential, and costs more up front, because it is physically different, more complex, larger and more accurate. In ways that are not always obvious to customers, tooling impacts quality, repeatability and capacity. Launching a critical program with average tooling is like swinging a baseball bat with one hand: you may still be able to hit the ball, but at some point, the weakness and lack of consistency will show.
High-Performance Castings
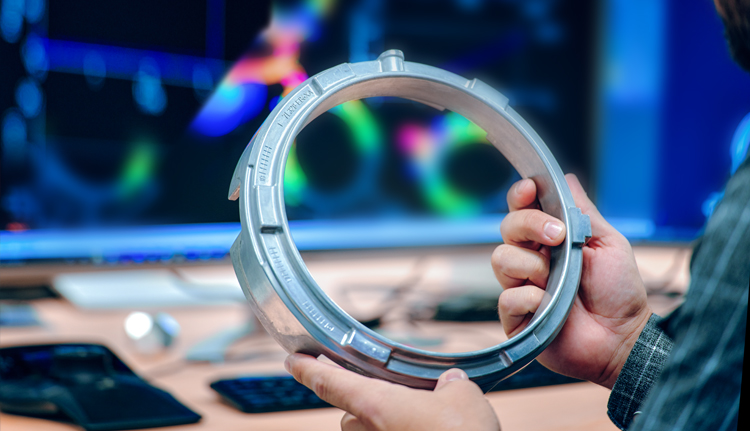
TOOLING REPLACEMENT
High-volume production of castings strongly benefits from including cavity replacement in the piece price, sometimes called “perpetual cavity replacement” or “continuous cavity replacement”. It is not a payment method for replacement tooling: it is a business model, bundling a service, a product and an insurance, that transfers the responsibility and risk of tool wear to the die caster. In addition, it provides the die caster with needed flexibility in choosing the appropriate time to build and certify replacement tools. Being focused on supply reliability, we typically have replacement tooling in the pipeline long before the current tooling is worn out, which is one more way we can be the strongest link in your supply chain.
high-performance tooling
WE DO NOT DESIGN, MANUFACTURE, OR USE ANYTHING THAT WOULD BE DESCRIBED AS “REGULAR TOOLS
Vacuum Assisted Die Casting
SPECIAL TOOLING CHARACTERISTICS
For one, 100% of tools in use at AMT are operated with at least standard vacuum assist. We have a lot of experience with leak-tight dies that help reduce gas pressure in the cavity and reduce flash. We can also engineer and make dies with advanced features, such as:
Multi-cavity tools with several sliding cores per cavity
Three-plate dies with central injection or hybrid injection (combining lateral and central)
3D-printed, conformal cooling and other advanced thermal management features
Complex, non-cylindrical replaceable inserts to improve die life and part quality
Extended die life through surface coatings and improved thermal management