Die casting technology meets know-how from the trenches
The A+ process includes many advances based on in-depth experiments over long periods. A single process improvement will rarely provide its full benefits without further developments to keep things in balance.
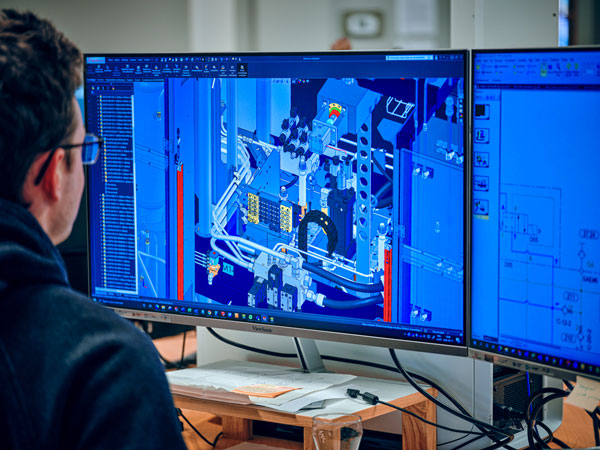
Most die casting equipment and tooling suppliers are not die casters themselves
They have a limited ability to evaluate the potential of their own products, as they mostly rely on customer feedback. It is therefore rare for suppliers to be able to provide true guidance on how to optimize use of their products. To benefit from off-the-shelf equipment, die casters must often go beyond what is offered and be willing to optimize the technology on their own.
Die Casting Technology
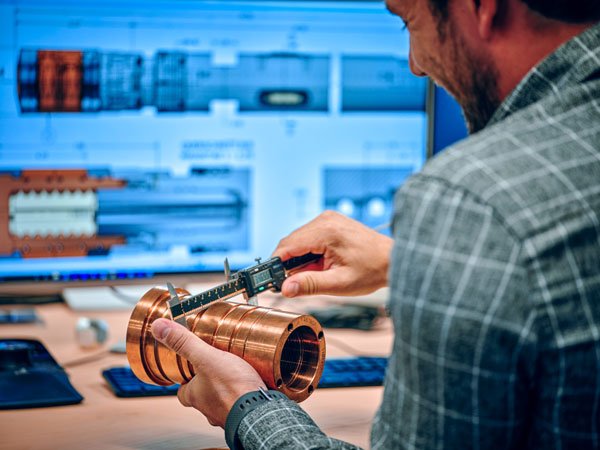
Innovation as a business model
Manufacturers must adopt new technologies to remain viable, and most achieve that by purchasing equipment and systems, following industry trends. For us, it has never been enough.
Our relentless pursuit of process excellence was key to our survival during tough times, and it enabled quick growth thereafter. Now more than ever, we invest on a continuous basis to remain a relevant manufacturing partner over the long run.
AMT A+ process
Examples of innovation by AMT
Advanced thermal management
Removing more heat from the die to improve productivity is relatively easy. Doing it while also improving quality is another story. AMT process engineering includes use of conformal cooling, spot cooling, high-pressure water cooling that make it possible to both improve quality and productivity.
High-efficiency, multi-cavity shot design
Traditional shot design for multi-cavity die tends to favor matrix placement of parts. This results in big runners, filling patterns that lack symmetry in space and time, less favorable heat dispersal. AMT’s approach makes shots lighter and more favorable to process quality.
Die sealing and gas evacuation
Die pressure tightness is an underappreciated factor of process quality. Allowing dies to “run loose” and slightly open to let air out is an old trick, but it comes with several shortcomings. Loss of pressure and lack of accuracy in shot control inevitably translates into reduced quality.
A quality process requires gases to be removed from the cavity in a controlled way, using vacuum and carefully positioned air outlets. Of course, the die and cold chamber need to remain pressure tight. AMT has developed both die design that make that possible, and process control to monitor deviations.
Continuous melt filtering
For a very long time, AMT has been using melting/holding furnaces with continuous filtering. This system ensures better metal quality, improved fluidity and die filling, as well as alloy flexibility.