
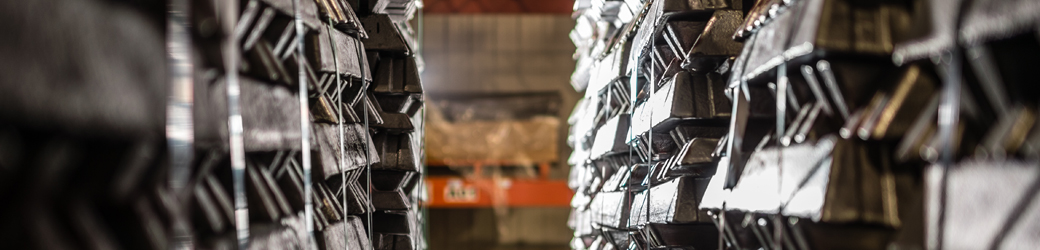
The pressure from society and legislation to become more environmentally friendly – and specifically to reduce the carbon footprint – is growing, and the die casting industry is no exception. Much of the carbon footprint of most castings comes from the metal that is cast – especially if it contains or is made entirely from primary aluminum, which is known for its high carbon footprint. In a die casting plant, the melting stage often accounts for more than half of the company’s (and ultimately the product’s) carbon footprint (Scope 1 & 2[1]) – and thus the largest portion entirely under the control of the die casting facility. It is therefore extremely important to maximize process efficiency and internal recycling, as well as furnace efficiency.
According to the International Aluminum Institute (IAI), the global average footprint of primary aluminum is estimated at 16.8 t CO2e / t Al (IAI Level 3[2]/ Scope 1-3 GHG Protocol Corporate Standard[1]) – the exact value can range from less than 4 t CO2e / t Al for “low carbon” primary aluminum made for example from hydropower with the latest smelting technologies to more than 20 t CO2e /t Al if it is produced from coal fired electricity. The carbon footprint of secondary foundry ingots (if made from near 100% post-consumer waste) is between 0.6 and 1.2 t CO2e / t Al).
In the casting plant, melting aluminum in a furnace is the most carbon-intensive process. The type of furnace is often determined (or at least strongly influenced) by the size of the casting plant and the number of alloys being cast.
Several studies have been conducted on this topic, including a comparison of deck furnaces and reverberatory furnaces – the most common types of furnaces in large foundries[3] In our case, that of a rather small die casting foundry that casts several different alloys, the most practical choice is crucible furnaces on each diecasting machine for both melting and holding. Regardless of the type of furnace, however, switching to electric furnaces and using renewable energy as the power source are the most effective ways to minimize the carbon footprint, with many positive side effects such as cleaner metal, reduced melt loss, less noise and heat in the plant, much lower emissions. The limiting factor is usually the power available in the facility – and of course the source of electrical power and costs versus gas.
TYPES OF FURNACES AND ENERGY SOURCES
For aluminum melting, the most common types of furnaces used in diecasting plants are gas-fired tower furnaces (also known as battery/shaft melters), reverberatory furnaces (dry and wet hearth, gas or electric), and crucible furnaces (gas or electric resistance or induction). Gas-fired tower and reverberatory furnaces can be large and central to feed multiple holding furnaces via a trough or bull ladle, or individual on each machine (for both melting and holding). Gas-fired furnaces generally have higher melt loss and often also lower melt quality than electric furnaces, as the metal is often exposed to flames and combustion products. While gas-fired furnaces often seem to be the “default” choice for many die casters, electric melting clearly has its advantages, not only when it comes to reducing the carbon footprint (depending on the source of electrical power[4]), but also in terms of melt quality, clean air and improved working environment[5]. The following table shows typical values for melt loss, energy efficiency (these can vary depending on many factors, so relatively wide ranges and an estimated average are shown) and carbon footprint with given (published) emission factors.
Comparison of furnace types with different energy sources with respect to their melt loss, energy efficiency and carbon footprint
(click to enlarge)
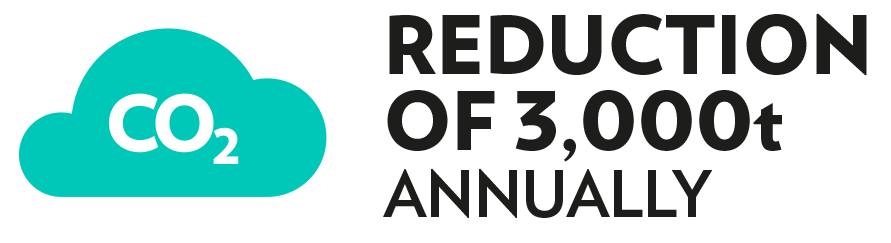
ENERGY SOURCE AND CARBON FOOTPRINT
The most common energy sources for melting and holding furnaces are gas and electricity. According to the U.S. Energy Information Administration (EIA), burning natural gas to produce energy results in fewer CO2 (and other) emissions than burning coal or petroleum products to produce an equal amount of energy. Approximately 117 lbs. of CO2 are produced per million British thermal units (MMBtu) equivalent of natural gas, compared to over 200 lbs. of CO2 / MMBtu from coal and over 160 lbs. / MMBtu from distillate fuel oil. If a mold caster does not have natural gas and uses propane instead, the result is 139 lbs. / MMBtu, which is slightly less than natural gas.[6] Other sources show even higher numbers, but the relationship between them is very similar. If a melt and hold furnace is run on electricity, the carbon footprint will depend on the source (or mix) of energy available. In the case of AMT Die Casting in Quebec, Canada, the only available source of electricity is 100% renewable energy, mostly hydro, which corresponds to a virtually zero carbon footprint (some would say it is still very low – so we used 0.5 g CO2/kWh, a value published by Hydro Quebec for 2020). Therefore, it is the obvious choice to minimize the carbon footprint of castings. In other provinces/states, a detailed comparison between different energy sources for electricity and their respective carbon footprints would be required – as well as possibly negotiating with the power company to source lower carbon footprint energy (potentially at a premium). Table 1 clearly shows that switching to electric power only offers the full benefits of a lower carbon footprint if a renewable energy source is available, but in the case of a crucible furnace, it is clearly the best option by far, as the relatively low energy efficiency makes the gas crucible furnace much worse than gas chimney or reverberatory furnaces. A typical gas reverberatory furnace gives an average of about 0.2, while a gas chimney furnace gives 0.14 tCO2e/t Al, a gas crucible will give an average of 0.52 (in the case of propane, almost 0.6 and oil, even 0.72) tCO2e/t Al castings. An electric crucible furnace with renewable energy source allows a reduction of more than 99% to only 0.0003t CO2e/t Al castings.
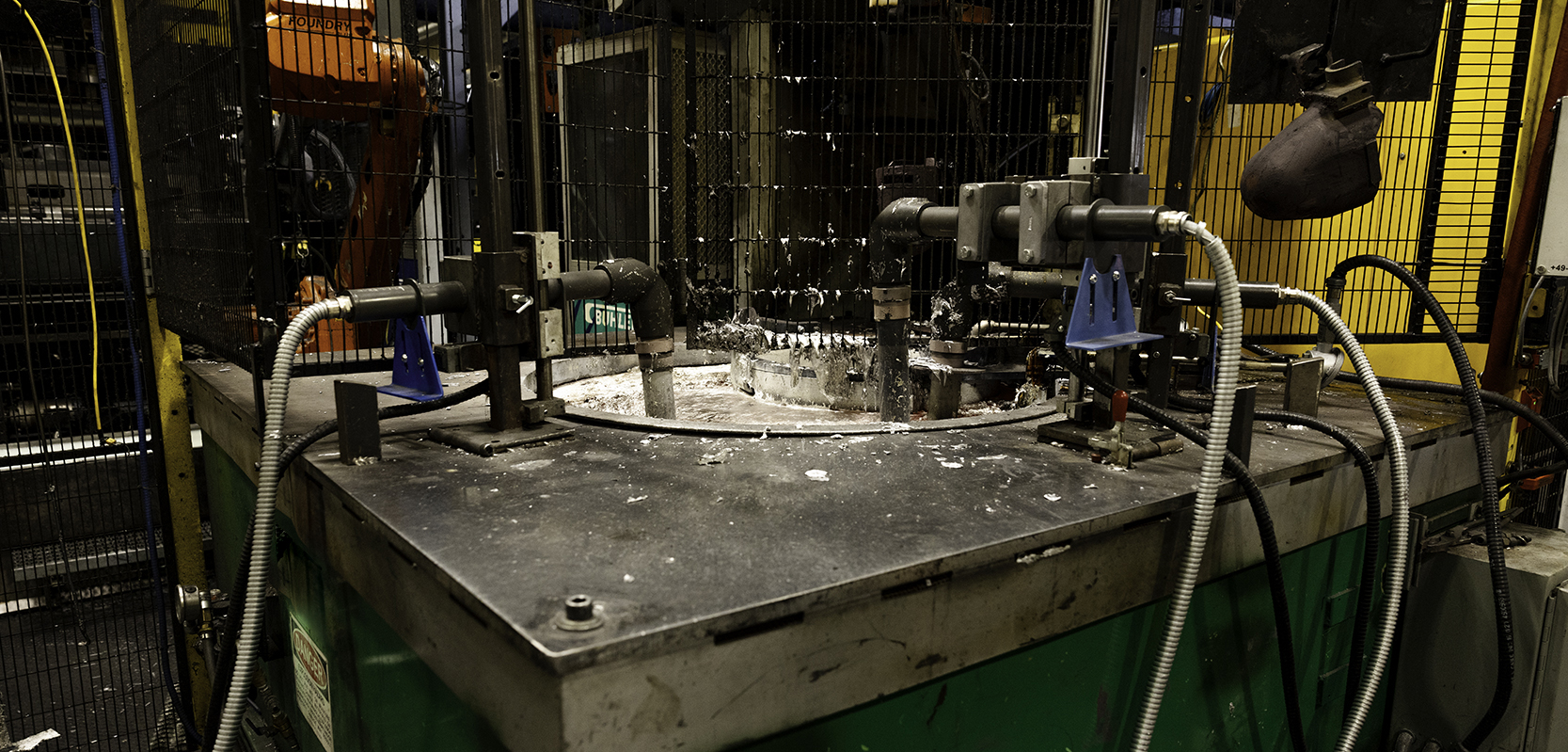
AMT’S CARBON FOOTPRINT
When calculating the carbon footprint of a company or product, CO2 emissions are categorized into scopes 1 through 3. Scope 1 consists of direct emissions, such as gas combustion, and scope 2 consists of indirect emissions that come from the production of electricity used by a company. Scope 3 consists of all indirect emissions from the entire value chain, including emissions from incoming materials and transportation. This Scope 3 will be similar at die casters and therefore will not be considered in the analysis of AMT’s carbon footprint reduction initiative. For each specific product and project, the metal with the lowest carbon footprint will be determined and used. For die casters, the melting stage represents the majority of their Scope 1 and 2 carbon footprint. Therefore, the energy source and furnace type used for melting will determine a large part of the company’s and product’s carbon footprint. The carbon footprint of a typical die caster is approximately 0.5 tCO2e/t Al in scope 1 & 2. Prior to switching to renewable energy, AMT used propane-fueled crucible furnaces and had a carbon footprint of approximately 0.6 tCO2e/t Al in Scope 1 and 2, which is above average, even though renewable energy (electricity) was used for all other energy needs. After switching to electric furnaces powered by Hydro Quebec’s renewable energy, the carbon footprint of AMT’s smelting in Scopes 1 and 2 dropped to 0.0003 tCO2e/t Al (using Hydro Quebec’s official emission factors). The carbon footprint of each casting, after taking into account all three scopes but excluding metal, consumables and logistics, is now approximately 0.00156 tCO2e/t Al, which is less than 0.5% of an average North American die casting.
conclusions
Previously, AMT Die Casting used primarily oil and propane-fired crucible furnaces, which generated a significant carbon footprint – typically in the range of 0.5 – 0.7 t CO2e/t Al. After some development work, electric crucible furnaces with integrated immersion heating elements were introduced. By using renewable energy sources (mainly hydroelectricity) for electricity, it was possible to almost completely eliminate this carbon footprint (more than 99% reduction).
Since the melting steps typically account for more than 50% of a die casting company’s carbon footprint, switching to electric crucible furnaces (melting and holding) has almost completely eliminated the company’s footprint and reduced the product’s carbon footprint by over 99% (Scopes 1 and 2), which reduces the full carbon footprint (Scopes 1 – 3) of our castings by half when made from secondary aluminum.
AMT Engineering and Tooling teams in collaboration with Mr. Martin Hartlieb, Viami International Inc. | ©2021
_______
REFERENCES:
[1] The Greenhouse Gas Protocol. A Corporate Accounting and Reporting Standard.
[2] Aluminium Carbon Footprint Technical Support Document
[3] J.R. Brevick, A.F. Mount-Campbell, C.A. Mount-Campbell, A.J. Horn: A Model for Alloy and Energy Use in High Volume Die Casting, Die Casting Congress & Exposition proceedings, 2012.
[4] D.W. White: Electric Melting: The New “Green Technology” Furnace. 2011 Die Casting Congress & Tabletop proceedings, 2011.
[5] F.B. Smith, R.P. Dathe, M.R. Smith: Bringing Back Electric Melting, 2011 Die Casting Congress & Tabletop proceedings, 2011.
[6] Natural gas explained.
_______
FIND OUT MORE | AMT Innovation | AMT Expertise | AMT Engineering |
_______