SEVERAL CHALLENGES COMBINED IN A SINGLE PART
Years ago, we realized that cosmetic class-A requirements are challenging for multiple aspects of the die castings process. From tooling to lubrication parameters, to vacuum performance and alloy choice, not much can be left to chance, especially for chrome-plated parts. Since chrome plating acts like a magnifying glass on any defect, surface finish of the castings has to be flawless. On top of that, this specific cosmetic casting is used for powertrain applications and requires leak tightness.
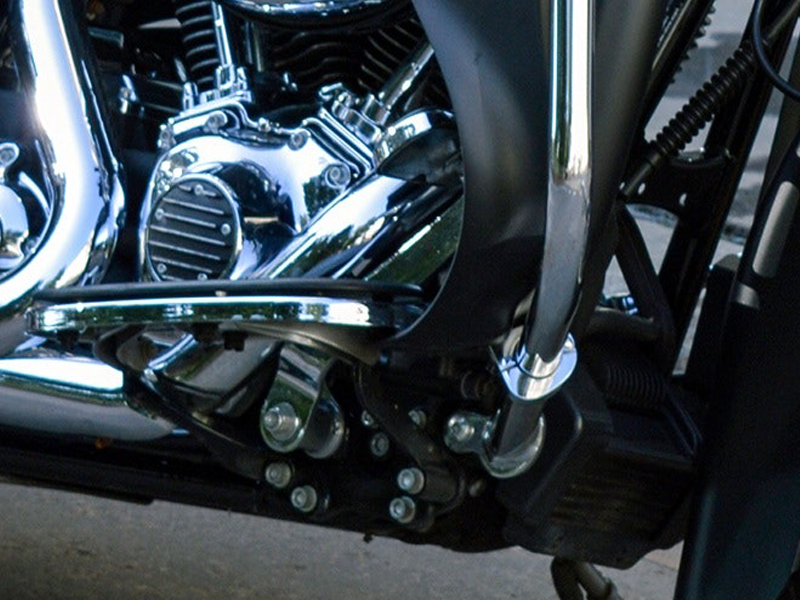
Since chrome plating acts like a magnifying glass on any defect, surface finish of the castings has to be flawless.
AMT TOOLING, PREDICTABLE QUALITY OVER THOUSANDS OF SHOTS
Tooling always plays a significant role in the success of a project, but for cosmetic parts, that role is even more important. The casting surface finish can only be as good as the surface finish of the tool it’s made from. It’s one thing to make a nice shiny casting from a brand-new tool, it’s another thing to maintain that quality level over tens of thousands of shots. If you have been exposed to castings with high cosmetic requirements, you know any small tool defect will quickly become a problem. The tool for this part was initially made with special techniques including mirror polishing, followed by strict maintenance. Specialized equipment, such as laser micro-welding, helps maintain part quality without hurting tool life like conventional welding would. Designing and building tooling in-house has definitely played an important role in our success with this part.
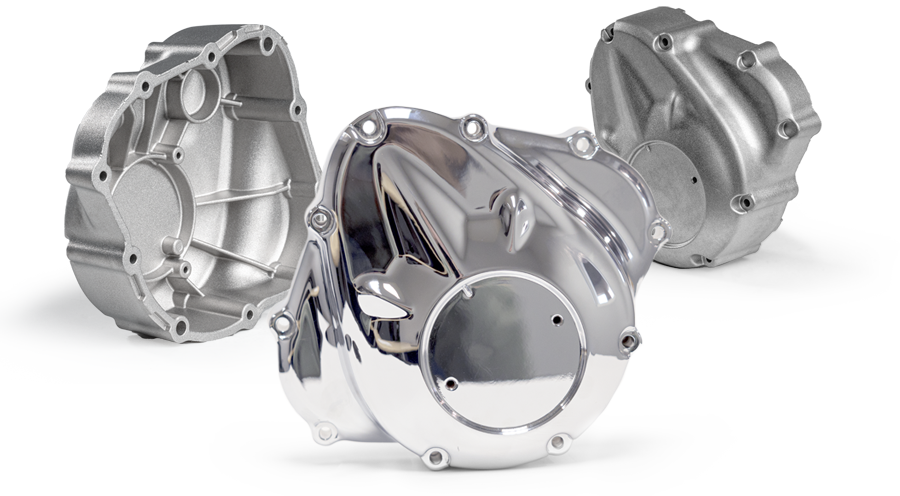
THE A+ PROCESS
Once we established the right tool design strategy, we had to adapt our process to strike a balance between surface finish quality and die wear. That is where good vacuum process helped achieve both targets, by allowing injection speed and pressure to be reduced, maximizing tool life without compromising part quality.
Another parameter that also takes on a new dimension is die temperature management. While it is normal for a die caster to take that aspect into consideration, cosmetic parts need to be approached differently. Some common casting defect such as faint flow lines or light soldering must not only be minimized but eliminated completely. At AMT, advanced technologies, like 3D printed conformal cooling, high-performance die coating and high-pressure spot cooling, were used to ensure years of trouble-free production of yet another challenging part.
AMT Die Casting | ©2021
_______
FIND OUT MORE | AMT Difference | AMT Expertise | AMT Engineering | AMT Tooling | Product Powersports |
_______