What it takes for a high-pressure die cast part to be weldable?
Historically, high-pressure die-cast parts were considered non-weldable, and rightfully so. Gas porosity, various other foundry defects and trapped impurities prevented clean and sound weld joints.
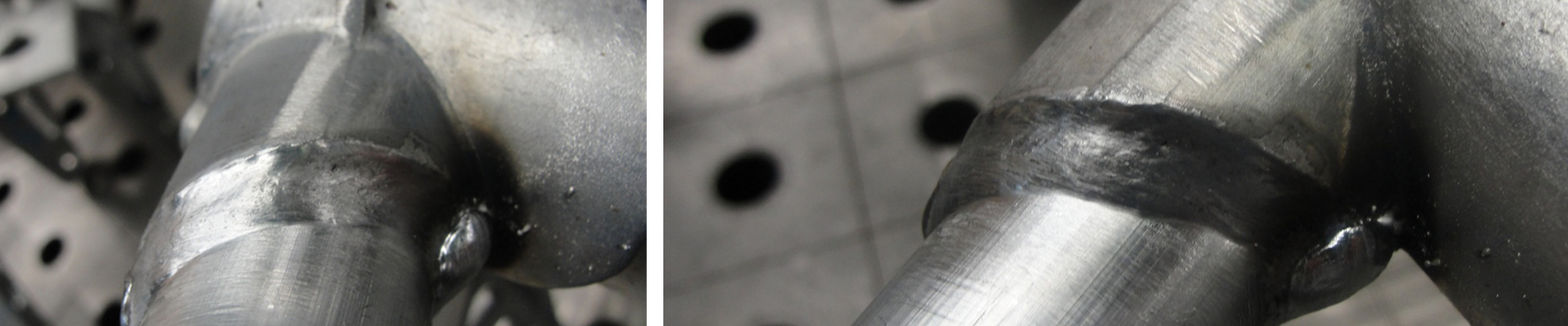
Many years ago, when a customer approached us, asking if we had the ability to convert an existing gravity-cast part to the high-pressure die-casting process for a weldable part, we knew what the challenge was.
To complicate things, some machined features had to become “as-cast.” Furthermore, the customer wanted to retain existing welding equipment and leave the welding process parameters unchanged. On top of that, all of this had to be implemented as a running change with very little development time! Thankfully, we were already producing heat-treated, high-vacuum parts, so we had a great starting point. After preliminary tests, however, we soon confirmed that it takes more than only powerful vacuum to obtain the required part integrity for weldability. Metal cleanliness, metal handling, lubricant choice and tool thermal management are some of the parameters you need to control better, along with reaching an extreme level of vacuum, to create a weldable part.
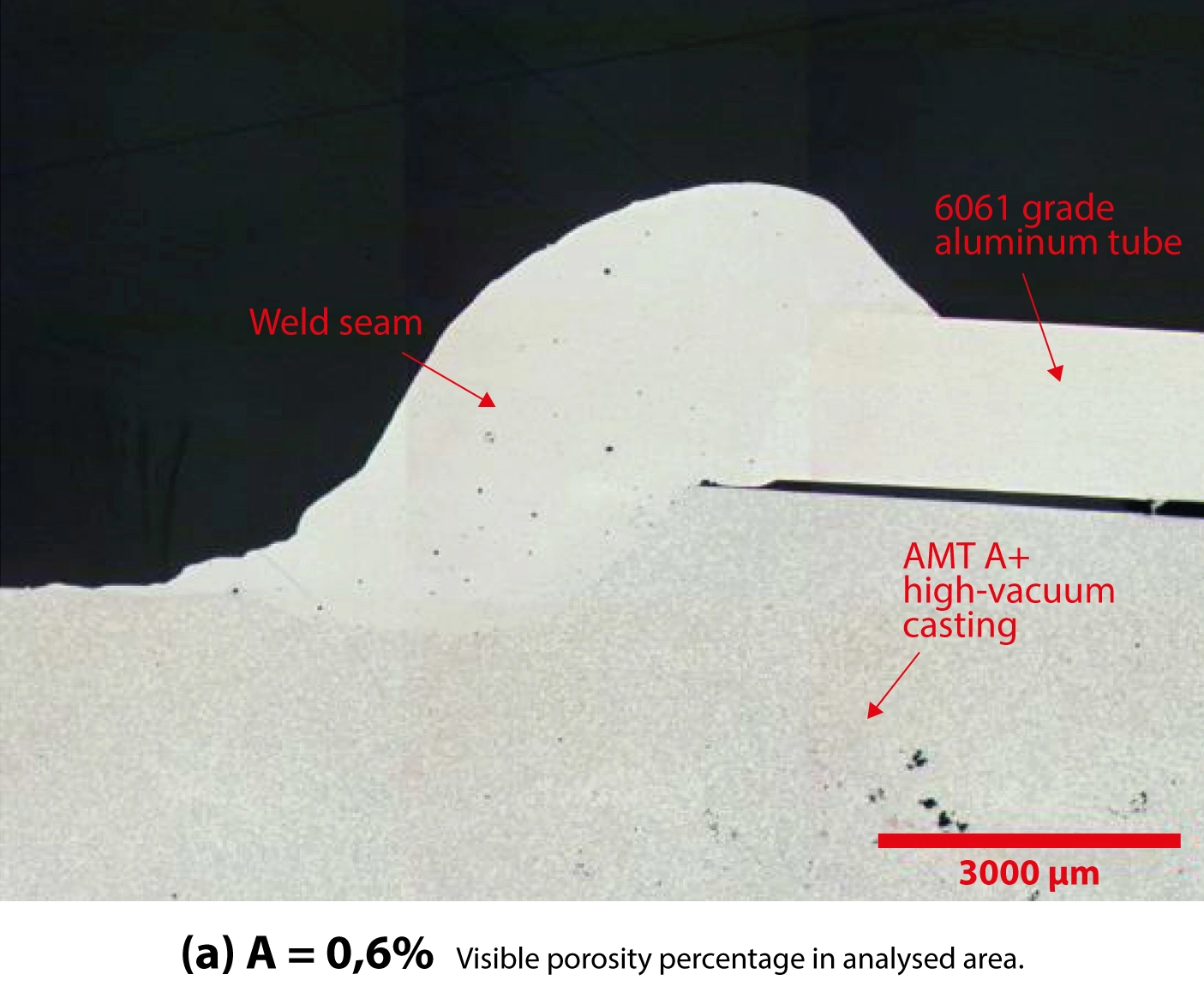
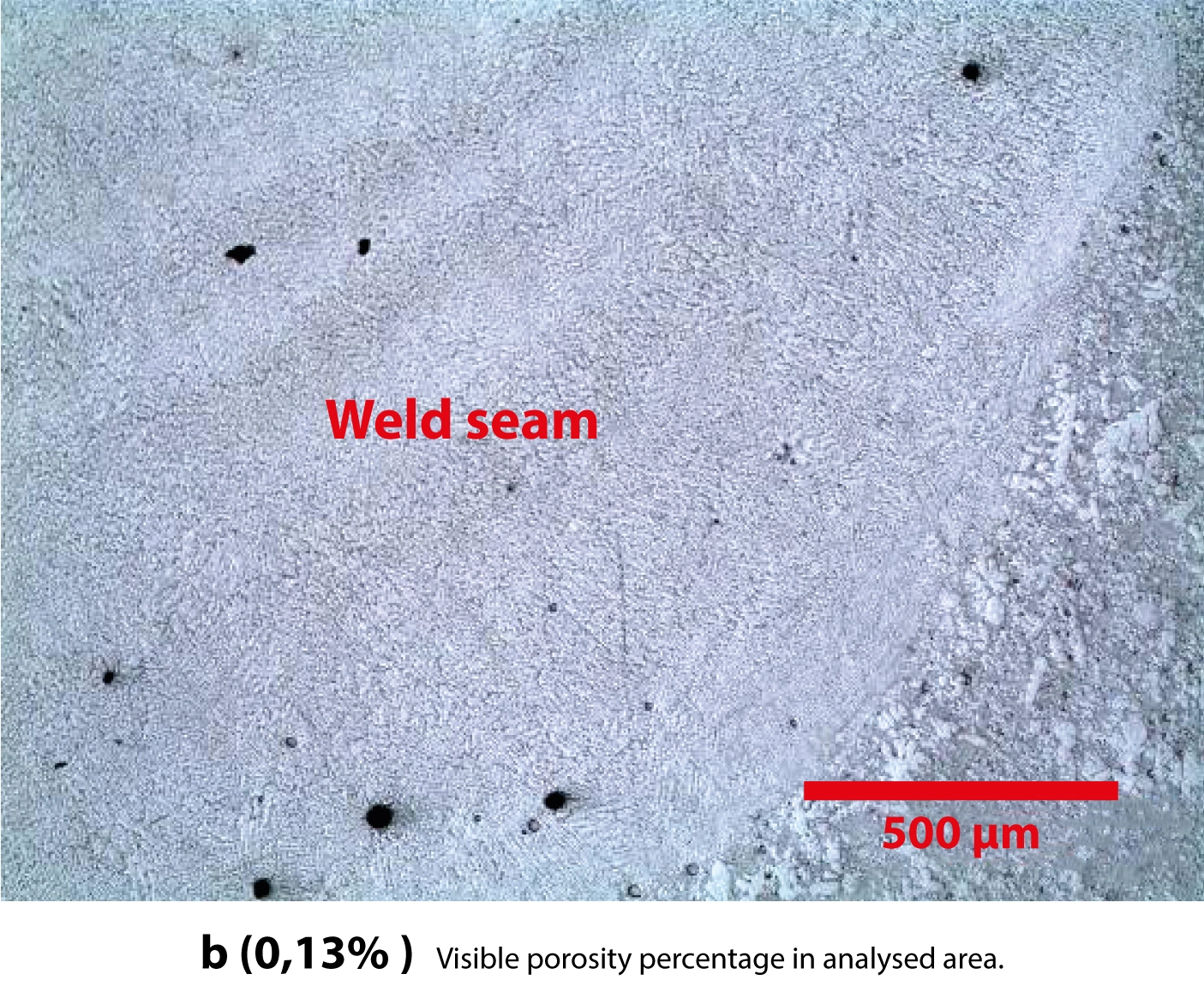
The Ultimate Test: A Defect-Free Weld Pool
Fusion welding a casting can be seen as the ultimate quality check because this process will, by nature, reveal any defect present in the part. It was especially true in this case since the customer was using a robotic, high-power MIG process that exposed parts to a lot of heat. That is where the process robustness philosophy of AMT paid off. Not only did we develop a successful process in a short period of time, but also made it reliable and repeatable very early on. This was critical as the running change scenario did not leave much time for a learning curve.
Mission Accomplished
At the end of the day, we were able to provide our customer with an outstanding quality casting that allowed them to perform a significant running change with no downtime. Thanks to AMT’s eagerness to push the limits, several technological innovations were introduced to the A+ process. Of course, none of this would have been possible without trust in AMT’s ability to deliver. The commitment and support from the customer who performed validation tests and provided valuable and timely feedback were key in the success of this project.
We are very proud to report that after several years of production at full volume, representing over 500,000 parts, there has been no fallout associated with casting weldability.
It’s no wonder AMT won NADCA’s Casting of the Year award in the most coveted category: High-Integrity.
AMT Die Casting | ©2021
_______
FIND OUT MORE | AMT High-Integrity | AMT Expertise | AMT Engineering | AMT Tooling |
_______